Lösung für Service- und Wartungstechniker
Aktuell fehlt es im Bereich der Produktion an einer praktikablen, verschlüsselten, nachverfolgbaren und manipulationssicheren Lösung zur Ablage von Messdaten bzw. produktionsnahen (Maschinen-) Daten. Für eine smarte Datenwirtschaft ist diese Ablage aber entscheidend, um zu einer praktikablen Datenverwertung durch nachgelagerte Analysen zu gelangen. Das Konsortium möchte durch die angebotene Lösung
- Service- und Wartungstechniker im Maschinen- und Anlagenbau bei der Dienstleistungserbringung unterstützen,
- den Maschinenbetreibern bzw. Dienstleistungserbringern Rechtssicherheit ermöglichen.
- durch die Entkopplung von Maschinenstandort und Leistungserbringung des Dienstleisters sowie durch neue Geschäftsmodelle den Beschäftigten eine ausgeglichenere Work-Life-Balance durch weniger Dienstreiseaufwand ermöglichen
Double-Ball-Bar-Messsystem
Ein Double-Ball-Bar-Messgerät (DBBM) kommt für die Genauigkeitsprüfung von Maschinen zum Einsatz. Es erlaubt die Durchführung von Kreisformtests nach ISO 230–4 zur Ermittlung der Abweichungen des Werkzeugnullpunktes von einer idealen Kreisbahn in einer Ebene. Mit der Auswertung dieser Abweichungen können mögliche Ursachen ermittelt und im Anschluss gezielt behoben werden.
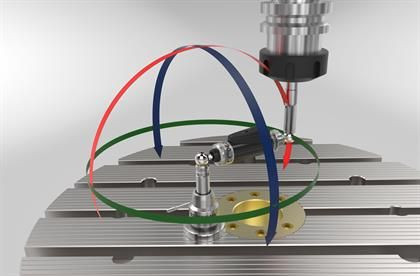
Im Vergleich zum Kreisformtest sind für die Kalibrierung einer Maschine umfangreiche, komplexe Prüfungen notwendig. Diese müssen sowohl die Genauigkeit der Positionierung des Werkzeugnullpunktes in Ebenen als auch im Raum berücksichtigen. Für die Bestimmung notwendiger Kalibrierparameter müssen die Auswirkungen möglichst vieler Fehlereinflüsse in einem Messablauf ermittelt werden. Im Anschluss erfolgt eine modellbasierte Kalibrierung, in deren Ergebnis neue Kalibrierparameter bestimmt werden. Diese werden in die Steuerung der Maschine integriert und bewirken eine verbesserte Bewegungsgenauigkeit.
Für die Messfahrt einer Kalibrierung muss ein Messsystem einen im Vergleich zu kommerziell verfügbaren DBBM deutlich erweiterten Messbereich nutzen können. Erst dadurch kann der gesamte Arbeitsraum der Maschine messtechnisch untersucht und in die Ermittlung der Kalibrierparameter einbezogen werden. Ein an der TU Dresden entwickelter Prototyp eines DBBM mit einem solchen erweiterten Messbereich wird für den Einsatzzweck einer einfachen, schnellen und sicheren Messfahrt weiterentwickelt.
Die Kombination des DBBM mit erweitertem Messbereich mit einer räumlichen Messbahn ermöglicht die Aufnahme aller notwendigen Daten für eine Maschinenkalibrierung. Im Ergebnis steht ein einfach einzusetzendes, robustes Messmittel für die Ermittlung und Verbesserung der räumlichen Bewegungsgenauigkeit einer Werkzeugmaschine.
Messfahrt an einer 5‑Achs-Fräsmaschine DMU 80 eVo. Zum Einsatz kam das am Lehrstuhl entwickelte Double-Ball-Bar-Messsystem mit erweitertem Messbereich.
Räumliche Messfahrt an einem Pentapod des Projektpartners METROM. Zum Einsatz kam erneut das am Lehrstuhl entwickelte Double-Ball-Bar-Messsystem mit erweitertem Messbereich.
Augmented Reality-System
Im Rahmen des Forschungsvorhabens wird ein AR-Assistenzsystem entwickelt, um dem Endanwender des Double-Ball-Bars beim Vermessen einer Werkzeugmaschine bzw. eines Roboterarms eine Unterstützung zu bieten. Hierbei wird auf anwendungsdomänenspezifische Hardware zurückgegriffen, um eine spätere Übertragbarkeit und Anwendbarkeit in der Praxis zu gewährleisten. Das Ziel ist es, sowohl die einzelnen Komponenten des Double-Ball-Bar Messsystems markerlos erkennen zu können und für den Maschinebediener relevante Informationen vom OPC UA Server zur Maschinenlaufzeit während der Vermessung anzeigen zu lassen als auch eine Adaption sicherzustellen, um auch für weitere Smart Services darauf basierende Unterstützungsszenarien zu entwickeln. Dabei gilt es, die für den Bediener notwendigen Informationen bereitzustellen und in geeigneter Form auf einem Endgerät zu präsentieren. Hierbei liegt der Fokus auf dem Einsatz von AR-Brillen im Produktionsfeld, um die Handlungsfähigkeit des Maschinenbedieners durch handgeführte Zusatzgeräte nicht einzuschränken und dennoch technologiegetriebene Mehrwerte zu schaffen.
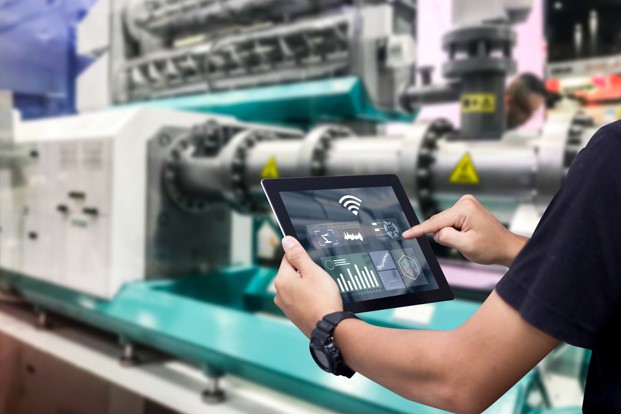
Im Pilot Use Case übernimmt die AUDIo-Plattform die Vermittlerrolle zwischen dem Maschinenbetreiber und dem Dienstleistungsanbieter. Die mit dem Double-Ball-Bar-Messsystem erfassten Maschinendaten und die darauf basierenden und durch den Dienstleistungsanbieter ermittelten Rekonfigurationsparameter werden mittels eines digitalen Service über die Plattform übermittelt.
Der Maschinenbetreiber kann diesen Rekonfigurationsservice über den Marktplatz beim Dienstleister anfragen und dabei aus verschiedenen Preismodellen wählen. Unterstützt werden beispielsweise die einmalige Ausführung oder ein Flatrate-Modell, welches die beliebige Anzahl an Ausführungen innerhalb eines bestimmten Zeitintervalls ermöglicht. Die Plattform informiert hierbei lediglich den Dienstleistungsanbieter über die Kaufanfrage des Kunden. Die eigentliche Vertragsabwicklung findet offline statt, um den individuellen Anforderungen der Kunden und des Dienstleistungsanbieters Rechnung zu tragen.
Nach der Freischaltung des Services durch den Dienstleistungsanbieter steht der Rekonfigurationsservice dem Kunden zur Verfügung. Der Service kann nun direkt über das Webinterface der AUDIo-Plattform in Anspruch genommen werden. Hierbei muss der Maschinenbetreiber die erfassten Messdaten und weitere Zusatzinformationen über das Webinterface auf die AUDIo-Plattform hochladen. Die Plattform informiert daraufhin den Dienstleistungsanbieter über das Vorliegen eines neuen Rekonfigurationsauftrags. Dieser kann nun die Rekonfigurationsparameter ermitteln und ebenfalls über das AUDIo-Webinterface an den Kunden durch die Plattform zurückspielen. Der Kunde wird ebenfalls durch die Plattform über das Vorliegen der Rekonfigurationsparameter informiert und kann diese nun von der Plattform herunterladen und auf die Maschine überspielen.
Sämtliche Daten werden dabei stets Ende-zu-Ende-verschlüsselt übertragen und die durchgeführten Prozessschritte im Distributed-Ledger IOTA manipulationssicher protokolliert. Hierdurch wird sichergestellt, dass nur der Kunde und der Dienstleistungsanbieter die im Rahmen der Serviceausführung erhobenen Daten lesen können. Die manipulationssichere Protokollierung ermöglicht Rechtssicherheit im Falle eines Rechtsstreits.